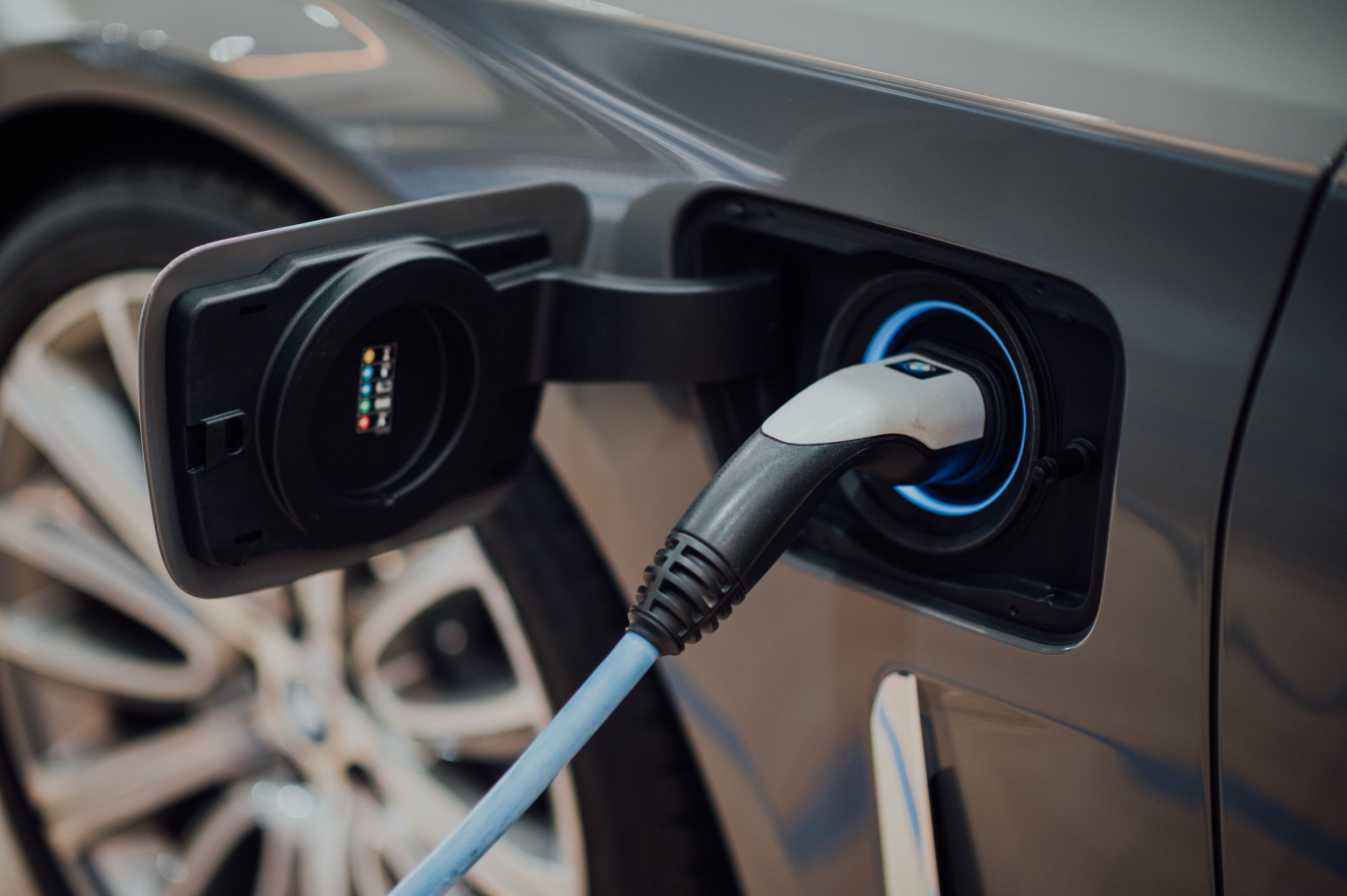
Agriculture
Part 4: Specialty Applications
Innovating Agriculture
Agriculture, like all sectors, is in a steady state of change. In this modern age, farmers, ranchers, and agricultural producers have an array of new electrified options to consider implementing to their benefit. This page illustrates a small subsection of emerging and established specialty applications that utilities should know about, from in-field intelligent support systems to more efficient processing equipment.
Moisture Removal
Tower-style radio frequency dryer vs traditional radio frequency dryer.
Radio Wave Grain Dryers
Radio wave drying systems, a new technology, are electrified solutions that use radio waves rather than heat to remove water from individual grains. This can reduce energy costs and improve grain quality by preventing over- and under-drying.
Traditional continuous cross-flow dryers (horizontal or tower-style) using propane or natural gas are versatile and dry a lot of grain very quickly. However, the typical grain dryer can waste as much as 40 percent of the energy it uses, according to a report from the Ontario Ministry of Agriculture, Food and Rural Affairs.
DRYMAX is a startup company looking to apply this technology to grain dryers, specifically classic tower-style dryers. Their Forcefield technology is designed to eliminate the need for liquid fuel and high heat drying The farming journal Successful Farming features an article discussing their patented technology.
More testing under more diverse conditions will aid in the acceleration of what appears to be a significant potential win for agriculture. Co-ops should use available data to share the benefits of this technology with agricultural members.
Specialty electric dryers utilizing infrared technology have also found their place in manure-drying operations. Systems like the BluTeq system, designed and built in the USA, have proven themselves as
industry leaders in providing machinery that allows farmers to confidently transform their pile of manure into pathogen-free material for easier management. Their machines take hundreds of pounds of manure at one time and process it within 30 minutes under an array of infrared heaters while being worked by augers. Dairies may consider this innovation for their operations to make the most of their time and energy.
Infrared Manure Drying
Manure management systems are a priority for farms keeping any livestock. Manure buildup can lead to serious hazards and hassle for large animal operations. Pathogens thrive in those environments, as do unpleasant odors. Infrared manure drying is an all-electric technology that farmers may consider for clean and efficient dairy management.
Syrup Evaporation
Out in the woods, maple syrup operators are considering new ways to improve their age-old process. By replacing traditional wood-fired boiler operations with efficient steam boilers, syrup producers make a more consistent product while lowering operating costs.
“Our operating costs are $4 an hour… for roughly 20 gallons of syrup,” says Eric Lively of Sunrise Farms in Massachusetts. “It’s been a really good investment. We want to go more energy efficient, and this is the way to go.”
Heating & Cooling
Heat Exchangers
Heat exchangers can effectively heat agricultural spaces, and may achieve efficiencies and fuel savings that fossil fuel heaters cannot. Electric heaters can be installed next to heat exchangers. This eliminates the requirement for long pipelines with heat losses during liquid transmission and boosts the overall efficiency of a heating operation.
Poultry, dairy cow, and swine facilities, as well as greenhouses can benefit.
These are rugged systems that can also address ventilation concerns like dust fouling.
Fresh air ventilation from heat exchange systems benefits farm workers, farm productivity, and overall animal welfare.
Heat exchangers are also an accessory to water heaters. They are self-contained and powered by the water heater's source. This application is useful for heating a water supply with a boiler system while otherwise keeping the systems separate.
Water Heating and Pasteurization
Consistent hot water is necessary for dairies, as facility and product hygiene are top priorities. Producing hot water through electric water heaters is a great choice for many dairy operations because of the cost savings over fossil fuel-fired heaters. Aging gas or oil-fired water heaters have a combustion efficiency of about 80% with standby losses of up to 3% per hour. Electric water heaters often boast a thermal efficiency of around 98% with standby losses as low as 0.3% per hour. Gas and oil-fired water heater tanks also present more safety concerns, making installation more challenging than electric water heater tanks. Electric heaters can be installed directly into the process line where heat is required, eliminating the need for extra steam or hot oil pipes.
The dairy industry is also beginning to electrify its pasteurization process. Instead of the traditional method of heating the product (typically with fossil fuels) to kill harmful bacteria, dairy processors are increasingly using ultraviolet light to pasteurize without the use of heat. This process consumes 92% less energy than other types of pasteurization while still eliminating the same amount of pathogens. UV pasteurization can also be used for juice, beer, wine, and other opaque liquids.
Air curtains installed at the Griesen’s family dairy in Wisconsin. Photo Credit: Berner Air Curtains
Air Curtains
It is challenging to keep large open-air facilities heated, but thanks to technologies like air curtains, these spaces can retain heat and keep insect infiltration down. Air curtains can be installed above any exterior entry in greenhouses and dairies to preserve the heat generated on site, and to encourage further ventilation of stale air. Replacing older gas-fired blower models with all-electric air curtains can be an easy way to lower a facility’s energy costs and use the existing heat best.
Greenhouse Space Heating
The space heating electrification potential in the greenhouse industry is higher than for all livestock buildings combined. This will only grow as the production of controlled-environment agriculture increases — particularly as legal cannabis comes to more states. A handful of electrification technologies are currently
Summary of Estimated Electrification Potential by On-Farm Activity
Intelligent Systems
Implementing modern technologies into today’s farming practices follows an age-old tradition of adapting tools for best use. These days, farms can utilize precision agriculture practices, allowing farmers to manage land, crops, and animals with more information to inform choices. Common elements of precision ag involve digital mapping, data analysis, farm modeling, and visualization.
Top soil mapping and analysis
Soil moisture sensors & weather stations
Intelligent fertilizer application
Orchard bloom and fruit analysis to assist nutrient strategy, pollination, irrigation, pruning, thinning and labor needs
On-farm applicant load management is only possible through electric systems. Utilizing programmable systems for HVAC, water heating, automated milking and feeders at dairies, and other high-usage applications can help farms prioritize labor and energy producers during periods of peak demand.
Additional Resources
USDA: Farm Energy Estimators
eXtension Farm Energy: Energy Efficient Hot Water for Farms
Washington State University Energy: Farm Energy Audit Checklist
Oklahoma State University: Comparative Energy Costs for Irrigation Pumping
Reinke: Precision Management
Absolute reports: Precision Ag report
SoCal Edison: Ag resources
Colorado Dept. of Ag: Farm Energy Efficiency Tools
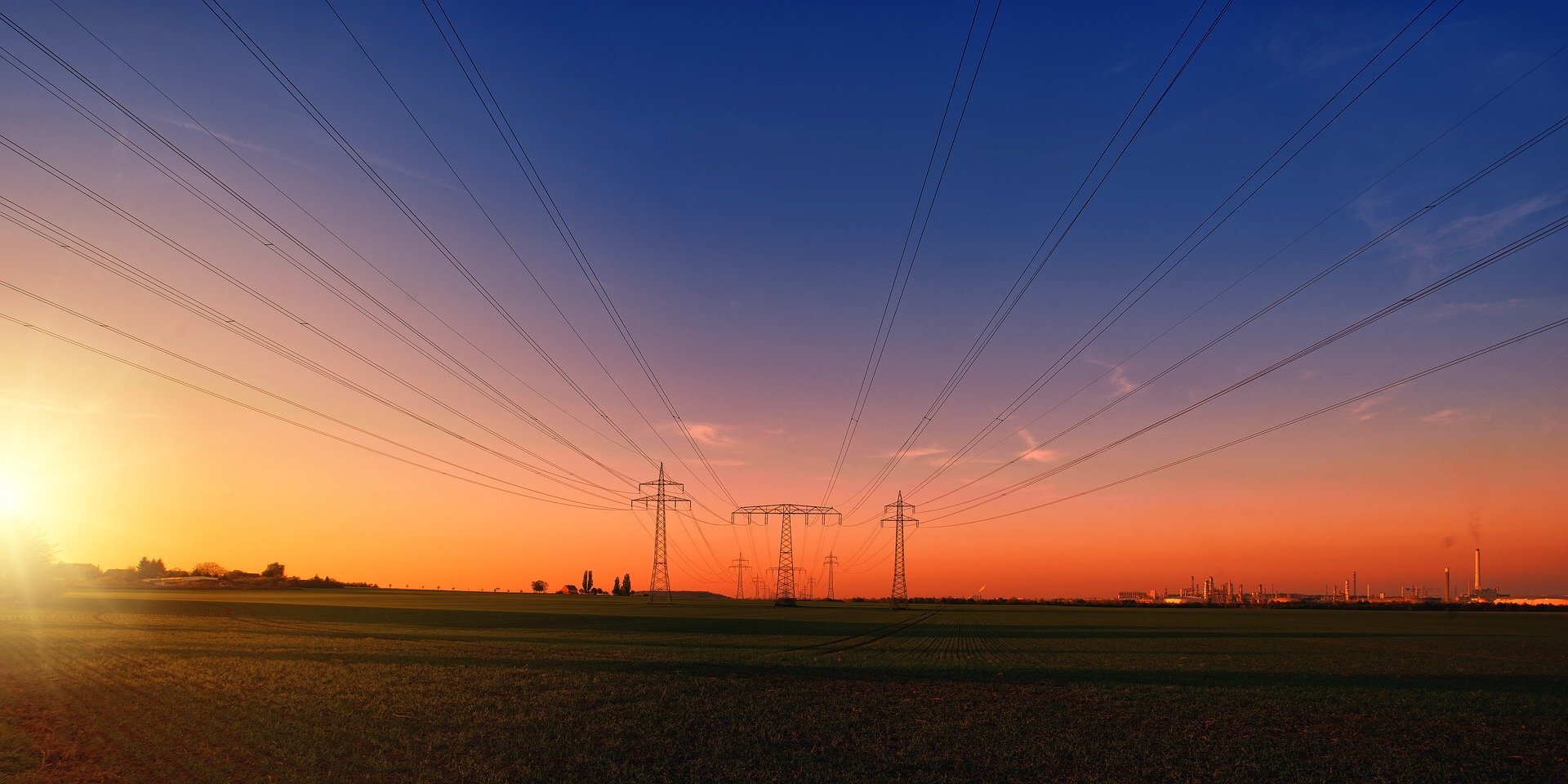