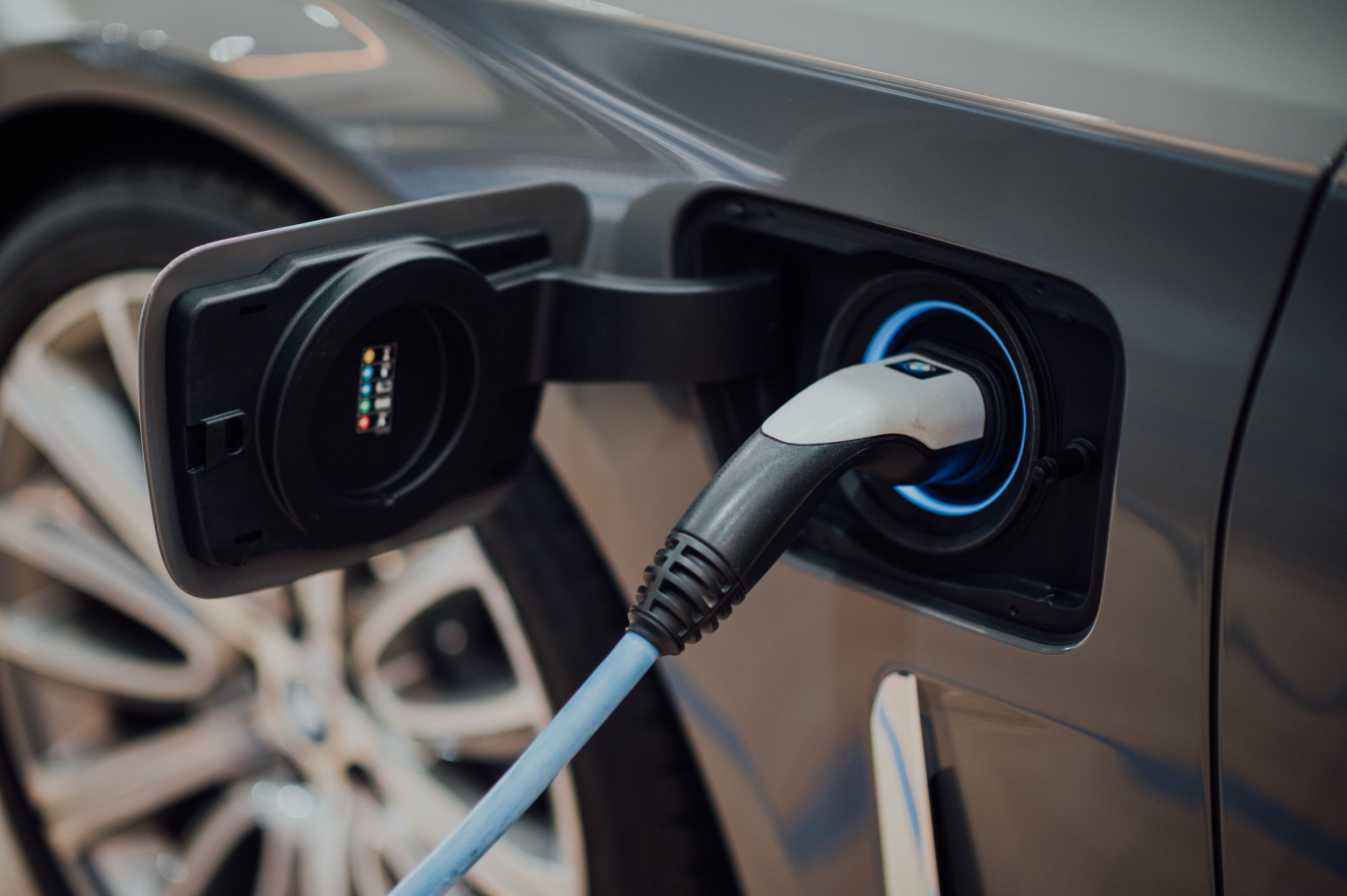
Industrial
Public and private capital is flooding into electrification. Industries are responding.
Electrified Industries
Industrial operations rely on an extraordinary amount of energy, accounting for one-fifth of global energy consumption. Electrification has the potential to greatly reduce the consequences and costs of industrial sector energy demand from extraction to manufacturing. According to a 2017 McKinsey study on global energy use, only about one-third of overall industrial energy is consumed as “fuel feedstock”, such as the petroleum that is used as the material base of plastics products. This indicates that electrification efforts should focus on the remaining two-thirds of industrial energy use which is known as ‘fuel for energy.’
Beneficial electrification can impact diverse processes, including those essential for the mining, automotive, aggregate, metal, plastic, and textile industries. As many industries transition and upgrade from fossil fuel-reliant technologies and embrace electrification, there are significant opportunities to reduce onsite waste and pollution, ensure operational reliability, and save money through more efficient practices.
Efficiency and lower energy costs can also be an angle for electric utilities to pursue meaningful programs with industrial customers, especially the small to mid-sized companies. Strong leadership from utilities across the nation will be key in bringing these benefits into the heart of America, and to these customers. Because industrial manufacturing demands immense amounts of energy, companies may seek to improve efficiency in order to control operating costs.
Getting It Hot
Injection molding machine. Photo Credit: Milacron
Industrial processes often demand extreme temperatures, which require high energy use. Increased electrification of manufacturing offers major opportunities for utility load growth while also creating potential load challenges. This balancing act may encourage utility managers to consider demand-response programs to curtail loads and incentivize customers to operate strategically.
Plastic manufacturing. Photo Credit: Ceramix Solutions
A key example of industrial electrification can be found in plastics manufacturing. These processes rely on a variety of high-intensity systems, like injection molding machines, extruders, and blow molding machines. Some manufacturers still opt for fossil fuel-based technology, however each of these systems can be run efficiently with electric machines. One noteworthy electric application is infrared heating used for thermoforming ovens to shape plastic products at scale.
Induction in the Automotive Industry
While electric vehicles may be changing the face of driving and fueling, the material components of automobiles can still be heavily reliant on fossil fuels, but this too is changing.
Innovation is giving electricity a new seat at the table when it comes to manufacturing steel, which is traditionally done through a gas- or coke-fired blast furnace. A new primary manufacturing process, which involves a method of using molten oxide electrolysis to reduce and melt iron ore with electricity, is being piloted by Boston Metals in Massachusetts. At scale, this technology would lead to significant electricity demand.
For materials arriving at an automotive factory, the secondary manufacturing process is about to begin, and with it an opportunity for electrification. Various components need to be formed and hardened past their primary manufacturing stage and induction heating is well suited to perform this task. Examples of induction can be found in manufacturing with annealing steel sheets, gear and camshaft hardening, or within brazing operations, which involve joining parts by melting a filler metal with a lower melting point than the base metal. Each of these processes involves heating the material to high temperatures before cooling it slowly to improve its strength and durability.
Induction heating is also being used in the production of electric motors, where it facilitates the assembly of copper wire windings. The use of induction heating reduces the time required for motor assembly and can improve the manufacturer’s precision.
While automotive manufacturing often relies on gas or coke-fired furnaces to achieve the rapid high heat necessary for steel hardening, this can change with the broader adoption of cleaner, more efficient electric technologies. With the use of induction, however, these temperatures can be reached quickly, cheaply, and emission-free with the use of electricity instead - a great example of beneficial electrification in practice.
Efficiency and cost effectiveness are motivating material industries, such as plastics and metal. As more industries consider efficient electrification, utilities can prepare to manage the inevitable demand in load to these high-energy customers.
Check out this great conversation between Volts podcast host David Roberts and Rondo Energy CEO John O’Donnell about why the electrification of industrial heating is a big step forward.
Keeping It Cold
On the other end of the thermostat, refrigeration remains a significant source of energy demand. Although refrigeration already depends upon electricity, the steady reliance from critical industries, such as medical and food service, upon this intensive energy need should prompt utilities to concern themselves with how they can better serve their clients and load growth, namely through improving efficiencies.
Industrial refrigeration can utilize variable frequency drives (VFD) to get the most out of their energy input. VFDs are important because they change the frequency of a signal to control the speed of a motor, and by doing so can save energy by not running the motor continuously. VFDs are used to control the speed of motors, fans, and compressors throughout industrial operations.
Industrial Emissions
Chemical manufacturing on St Clair River, Michigan. Photo Credit: Dennis McDonald, Alamy
New climate policies are putting pressure on major industries to reduce greenhouse gas emissions while also offering new cost and emissions savings through carbon markets. These efforts are designed to reduce industrial emissions while maintaining critical efficiencies. Government-supported investments in infrastructure and energy subsidies will continue to widen levels of adoption of technology that further allows for beneficial electrification.
Source: “Annual Energy Outlook 2021 with Projections to 2050,” U.S. Energy Information Administration, Feb. 3, 2021.
One of the surest pathways to lowering overall emissions is through beneficial electrification programs that promote fuel switching from fossil fuels to clean electricity. Beyond policies, the U.S. Department of Energy is stepping in to support and encourage the efforts of companies voluntarily pledging to reduce their energy intensity and industrial waste. DOE’s Better Plants initiative “aims to help leading manufacturers boost efficiency, increase resilience, strengthen economic competitiveness, and reduce their carbon footprint through improvements in energy efficiency.” Programs like Better Plants are built upon the basis that electrification can serve the customer, environment, grid, and overall safety.
Lowering Energy Costs
“We’re pleased with the way this has worked out. It is a lot better than a diesel engine, [there’s] less maintenance, and obviously we have a little bit higher electric bill but we have no diesel fuel expenses now.”
- Mike Vaughn, Superintendent, Charleston Stone Company
To the extent that anyone has skepticism about the power of electric motors, look no further than the electrification of rock crushing. The story of Coles-Moultrie Electric Cooperative’s partnership with Charleston Stone Company in Illinois is a great example of how to support rural America with the operational and cost-saving benefits of electrification.
A National Rural Electric Cooperative Association’s (NRECA) Tech Surveillance report from October 2017 details the cost savings of Coles-Moultrie’s electrification project with their customer. Previous to this project, the report states that the diesel engine being used likely operated at 35 to 45 percent efficiency. “The new electric crusher motor is 95 percent efficient,” states NRECA. “It only costs $1.04 for the electricity needed to run a 95 percent efficient electric motor that will provide the same output that a 35 percent efficient diesel engine will produce with a $2.50 gallon of diesel.” For many industrial customers, a 200% savings is hard to pass up for “business-as-usual”.
The electric and mobile Keestrack I4e Reversible Impact Crusher
Beyond the energy savings, operational costs can be spared through increased productivity. The Tech Surveillance report continues, “Mike Vaughn, who manages the operation at the quarry, estimates the cost to Charleston Stone is “$2,000 to $3,000 per hour in maintenance performed, wages, and lost productivity” when the primary crusher is down. The company was experiencing 80 to 120 hours of downtime annually, so eliminating this could save $160,000 to $360,000 each year.”
By switching from diesel machinery that was unreliable, noisy, and costly to an electric rock crushing company, the electric cooperative was able to sell more electricity to Charleston Stone, and Charleston Stone was able to operate more days. The adoption of electrified equipment in rural enterprises, such as the crushed stone industry, will help set a new standard for electrification investments that lower energy bills and boost productivity.
Improving Worker Safety
Photo Credit: MacLean Engineering
One of the immediate benefits of industrial process electrification is the removal of hazardous materials from worker operations. In mining and other industries, diesel engines and the associated particulates and fumes have long posed a serious threat to worker safety. Electric alternatives eliminate on-site emissions completely, greatly improving worker health. Additionally, electric motors produce far less waste heat energy than internal combustion engines, reducing the sweltering temperatures of pit mines and other enclosed sites.
The international mining industry is moving to adopt electrification throughout its operations above and below ground. The International Council on Mining and Metals, has pledged to eliminate diesel use by 2025 and to operate vehicles with collision avoidance technology. The transition away from diesel engines will also greatly reduce underground noise pollution — a key metric targeted by the industry to improve working conditions and overall site safety.
Market Outlook
The market for industrial electrification will continue to expand as governments continue to push for reductions in greenhouse gas emissions and companies pursue strategies to comply and reduce the climate impacts of their operations, particularly those that cut operating costs. In 2021, the First Movers Coalition was launched by the World Economic Forum as an effort to bring together corporate commitments towards buying zero-emission goods and services by 2030 in order to increase their cost competitiveness. The First Movers Coalition focuses on seven industries: shipping, aviation, steel, concrete, trucking, aluminum, and carbon removal. A total of 81 companies signed onto the First Movers Coalition including Apple, FedEx, Volvo, Amazon, PepsiCo, Microsoft, and General Motors.
Industrial electrification has been receiving renewed attention from the U.S. government. The Biden Administration launched the Industrial Efficiency and Decarbonization Office as a tool to fund research and development across manufacturing. The White House also announced new procurement standards under the “Buy Clean” program managed by the General Services Administration, which oversees $75 billion in annual contracts. This program seeks to encourage companies vying for lucrative government contracts to lighten the embodied emissions of their materials. The program has been praised by industry leaders, including the Alliance for American Manufacturing which stated, “A Buy Clean policy built upon existing Buy America requirements has the potential to boost American manufacturers and workers who are doing the hard work to build a cleaner industrial sector.”
Companies will take many routes to approach electrification. Most motivated companies are looking to team up with partners that will help them achieve their environmental goals in less direct ways, such as through waste mitigation or purchasing offsets. But many will investigate or install new electrification technologies into their processes.
According to a Deloitte Insights survey of industrial clients, the transition toward electrification has already begun. The report surveyed industrial manufacturers across multiple sectors who are stating they can achieve 45% overall electrification by 2035. Most of the surveyed manufacturers shared that these goals would be met by, “leveraging partnerships and joint ventures to transition toward a sustainable future,” while other respondents indicated their approach will be “outsourcing strategies with vendors and suppliers.”
Additional Resources
McKinsey: Plugging In: What Electrification Can Do For Industry
Applied Energy: Technologies and policies to decarbonize global industry: Review and assessment of mitigation drivers through 2070
US General Services Administration: What They Are Saying
Department of Energy: Better Plants
Electric Autonomy Canada: Deep secrets: How Canada’s mining sector grabbed the global lead in mining electrification
MINING.COM: ICMM introduces innovation roadmap for cleaner mining vehicles
Pit and Quarry: Comparing electric and diesel powered portable plants
National Rural Electric Cooperative Association: Electric Rock Crusher: 'It's Been Beneficial'
Tech Surveillance: Rock Crushing Equipment
Deloitte Insights: Electrification In Industrials
World Economic Forum: COP26: What is the First Movers Coalition?
Forbes: Near-Zero Industrial Emissions By 2050 Would Boost U.S. GDP 3.3%, Create 5 Million Jobs
Royal Society: Ammonia: zero-carbon fertiliser, fuel and energy store